Alcast Company Can Be Fun For Everyone
Table of ContentsFacts About Alcast Company UncoveredAlcast Company Things To Know Before You Get ThisThe Alcast Company StatementsAlcast Company Can Be Fun For AnyoneSome Ideas on Alcast Company You Should KnowThe Definitive Guide for Alcast Company
Chemical Contrast of Cast Light weight aluminum Alloys Silicon promotes castability by decreasing the alloy's melting temperature and improving fluidness throughout spreading. Furthermore, silicon contributes to the alloy's strength and wear resistance, making it valuable in applications where resilience is important, such as automobile parts and engine elements.It likewise enhances the machinability of the alloy, making it simpler to process right into completed products. In this way, iron contributes to the total workability of light weight aluminum alloys. Copper enhances electric conductivity, making it useful in electrical applications. It also boosts rust resistance and contributes to the alloy's total stamina.
Manganese adds to the stamina of aluminum alloys and boosts workability (Foundry). It is generally utilized in functioned aluminum items like sheets, extrusions, and profiles. The existence of manganese aids in the alloy's formability and resistance to splitting during construction processes. Magnesium is a light-weight element that supplies strength and impact resistance to light weight aluminum alloys.
9 Simple Techniques For Alcast Company
It allows the production of lightweight elements with exceptional mechanical residential properties. Zinc boosts the castability of light weight aluminum alloys and helps control the solidification process during spreading. It boosts the alloy's strength and hardness. It is commonly found in applications where detailed forms and fine information are needed, such as decorative spreadings and specific vehicle components.
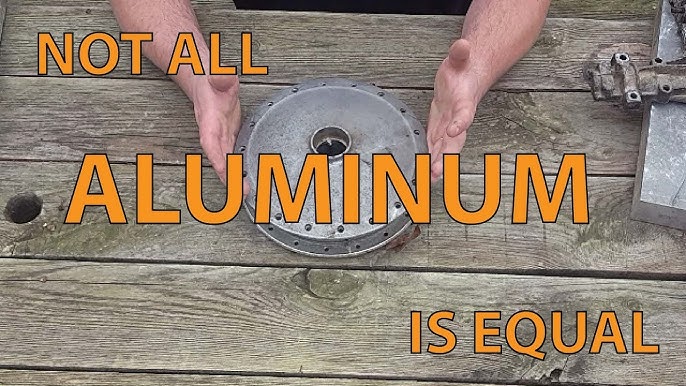
The primary thermal conductivity, tensile toughness, return strength, and elongation vary. Select appropriate basic materials according to the efficiency of the target product created. Amongst the above alloys, A356 has the highest possible thermal conductivity, and A380 and ADC12 have the lowest. The tensile limit is the contrary. A360 has the most effective yield strength and the highest prolongation price.
Alcast Company - An Overview

In precision spreading, 6063 is fit for applications where detailed geometries and high-quality surface coatings are paramount. Instances consist of telecommunication rooms, where the alloy's exceptional formability enables for sleek and aesthetically pleasing designs while keeping architectural honesty. In the Lighting Solutions sector, precision-cast 6063 elements produce stylish and efficient lighting components that call for complex shapes and good thermal efficiency.
The A360 exhibits premium elongation, making it ideal for complicated and thin-walled components. In precision spreading applications, A360 is well-suited for markets such as Customer Electronics, Telecommunication, and Power Tools.
Not known Incorrect Statements About Alcast Company
Its unique buildings make A360 a beneficial choice for accuracy spreading in these markets, improving product toughness and top quality. Light weight aluminum alloy 380, or A380, is an extensively used casting alloy with several distinctive qualities. It provides excellent castability, making it a perfect option for accuracy spreading. A380 displays great fluidity when molten, making sure complex and in-depth mold and mildews are properly replicated.
In accuracy casting, light weight aluminum 413 shines in the Customer Electronics and Power Equipment industries. It's generally used to craft detailed components like smart device housings, cam bodies, and power tool cases. Its accuracy is amazing, with limited tolerances up to 0.01 mm, making certain perfect item assembly. This alloy's premium rust resistance makes it an excellent option for exterior applications, ensuring resilient, sturdy products in the discussed sectors.
The Buzz on Alcast Company
Once you have actually decided that the light weight aluminum pass away casting procedure is appropriate for your job, a crucial following action is picking one of the most proper alloy. The aluminum alloy you choose will substantially influence both the spreading process and the properties of the end product. As a result of this, you should make your decision meticulously and take an enlightened technique.
Identifying one of the most appropriate light weight aluminum alloy for your application will certainly imply evaluating a wide array of features. These comparative alloy features comply with the North American Pass Away Casting Organization's guidelines, and we have actually divided them right into 2 categories. The initial classification addresses alloy features that impact the production process. The second covers features impacting the homes of the last product.
The Definitive Guide to Alcast Company
The alloy you choose for die casting directly affects a number of elements of the casting process, like exactly how simple the alloy is to function with and if it is susceptible to casting issues. Warm fracturing, additionally called solidification cracking, is a typical die casting defect for aluminum alloys that can result in inner or surface-level rips or splits.
Particular light weight aluminum alloys are extra at risk to warm splitting than others, and your choice ought to consider this. One more common defect located in the die spreading of light weight aluminum is die soldering, which is when the cast sticks to the die wall surfaces and makes ejection difficult. It can harm both the actors and the die, so you must try to find alloys with high anti-soldering properties.
Rust resistance, which is already a noteworthy attribute of light weight aluminum, can vary considerably from alloy to alloy and is an important particular to think about depending on the ecological conditions your check out this site item will be revealed to (Aluminum Casting). Put on resistance is another home commonly sought in light weight aluminum products and can set apart some alloys